Ecologic Battery Breaker and Separation
The most advanced system to break batteries, separate and recover the components
Presentation
Directly from our Italian long time experience on the field, we are presenting our lead batteries reciclying plants.
The environment safety and the reuse of the materials is now an obligation and a business opportunity.
This thoughts belong to all those people who want to preserve the nature, the increase the quality of life and to save and to earn money from waste.
All battery producers and cars disposal have this opportunity. A lot of them are already doing that and every day more and more people are asking to enter in this market. Also Governments are investing and financing the recycling of materials.
If we consider the reduction of mines, the sharply increasing cost for row materials, and the taxation for waste that goes up every day, we can confirm that recycle is worthwhile. In this particular aspect we can be useful and we can put in place our experience, know how and machinery.
Our lead batteries recycling plants are built on a simple concept: recycle the most part of the lead, the light plastic and the oxide past of the spent batteries.
In particular, this multiple unit is studied to be able to process the batteries in this way:
- empty the electrolyte, filter it and eventually concentrate it
- crush the batteries in small pieces
- separate the main components:
- grids and poles
- lead paste
- polypropylene
- heavy plastic (separators)
The crushing and the separation is done using the energy and the water.
The water is constantly reused so to reduce consumption. This allows the plant to be placed everywhere
The crushed pieces of batteries are washed to remove all sulphuric acid pollution:
- Lead, grids and poles, clean and with purity from 98% to 99%. They can be processed or sold
- Polypropylene washed. It can be sold
- Lead paste from grids, collected and drained (up to 14% w. content). It can be sold or processed
- Heavy plastic (agm and poliethilene separators, wood etc) collected to go to disposal
- Electrolyte filtered can be re-used or sold
MATERIAL BALANCE:
EXAMPLE WITH A LEAD BATTERY RECYCLING PLANT THAT CAN PROCESS 200 TONS DAY
weight materials (%)
55,6 – 27,8% grids/poles
72 – 36,0% paste S = 6,5%
11,2 – 5,6% polypropylene
16,4 – 8,2% Separators, PVC, Rubber,
44,8 – 22,4% electrolyte: as 85% water, 15% acid
T200 – 100,0% LEAD BATTERIES
You can calculate easily the ROI and the payback time only looking to lead market price*T day produced.
After this first part, complete and ecologically friendly, is possible to set up a unit with some kettles and/or a rotary furnace, to process the lead to have bullions and alloys.
This part depends on the factory layout, the quantity of battery that are monthly processed and the investment capacity.
We can support the customer to tailor the correct dimensions of the breaker, the separation station, the utilities, and the right shape of the rotary furnace with the kettles to produce alloys.

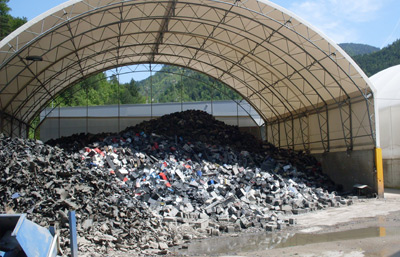